Linear compression spring
Linear compression spring, which is a spiral spring with linear constant force; It is a more common spring in the custom spring,We are very good at processing linear compression springs, in our spring outlet, occupy a certain proportion.
The difference between compression spring and tension spring:
Major difference | Linear compression spring | Linear tension spring |
Working principle and force direction | When subjected to downward pressure, the linear compression spring is compressed, thus storing deformation energy. There is a certain gap between the ring and the ring of the spring, and the spring shrinks and deforms when subjected to external load. | When not under load, there is generally no gap between the ring and the ring of the stretched spring. When the stretch spring is pulled apart, it tries to pull the two ends back together, creating a force that absorbs and stores energy. The tightness of this spring under tension or without tension determines the initial state, controlling the initial force to meet the needs of different conditions. |
Application field | Widely used in automobiles, construction machinery, home appliances, sports equipment, medical equipment, etc., mainly to provide resistance to external load pressure. | Widely used in defense, automotive, medical equipment and other fields, for connecting or fixing parts to provide resilience. |
Structural characteristics | Usually the distance between the spring ring is large,It is compressed when it receives an external force,To achieve the effect of shock absorption. | The ends are usually made of hooks,To ensure the tension source of the stretching spring,The circles are close together and remain so even when there is no tension. |
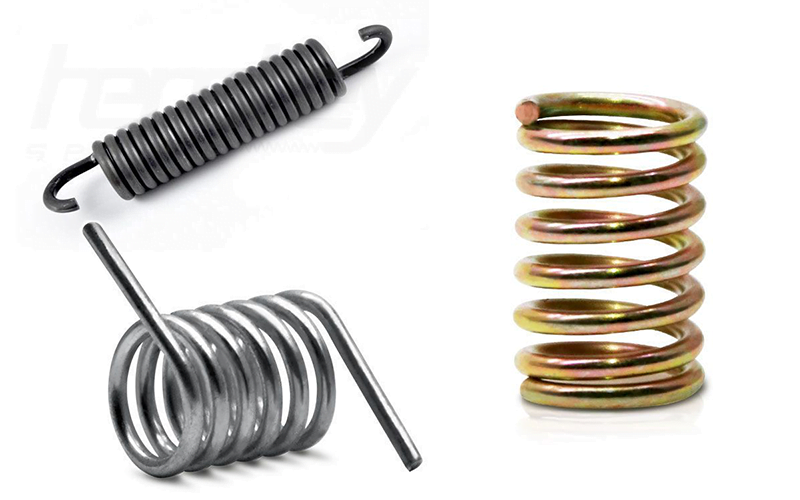
Linear compression spring
The Linear compression spring deflects in a straight line, whether it is vertical or horizontal. The amount of force they apply is based on physical dimensions such as wire diameter, outside diameter, free length, active coils (the space between active coils) and the type of material used. Some springs may be very similar in shape or size, but the forces they exert and their elasticity depend on the proportions of all the dimensions that make up a linear spring. This is due to stress factors such as the spring index or ratio within the number of coils (or the space between these coils) and the free length.
If your Linear compression spring has a tight index (a large wire diameter proportional to the outside diameter), it will be under pressure, so it will be able to carry a significant load, but may not be able to move (or deflect) much. The same is true when your spring has a long free length and very few coils. The opposite of these given examples (large exponents or many coils proportional to the free length) will give you the opposite reaction because it will be subject to less pressure: the spring will be able to deflect more, but it won’t be strong. The following formulas and examples show how this works.
Spring index (This formula applies to compression and tension springs)
The Linear compression spring index is the ratio between the diameter of the spring and the diameter of its conductor. To calculate the spring index, one must subtract a wire diameter from the outside diameter. The result is what we call the average diameter, as shown in the figure. Then you have to divide the average diameter by the diameter of the wire. The result is the exponent of the spring. A 4:1 index is too tight, and a 15:1 index is too loose, so you want to make sure you’re in between.
Linear compression spring index formula:
- Index = (Outer Diameter – Wire Diameter) ÷ Wire Diameter
- I = (OD – WD) ÷ WD
- Example: You have an outer diameter of 0.5” and a wire diameter of 0.05”.
- I = (0.5 – 0.05) ÷ 0.05
- I = 0.45 ÷ 0.05
- I = 9
- linear compression spring mean diameter formula
Linear extension spring
The extension spring also deflects in a straight line. Depending on their physical size, the amount of load applied to the spring is proportional to the spring travel because these springs exert a constant force. There is another value that a linearly stretched spring must pay attention to when performing load calculations. This value is called the initial tension. Initial tension is the energy that has gathered between the coils of your extended spring, thus keeping the coils tight together.
Once your extension spring is pulled close enough, you can see the light between its coils. This is an additional load that must be added to a load calculated using only the spring rate. To calculate the load, you must multiply the spring travel times the spring speed. This will tell you how much load you need to meet the required extension length. Once this value is calculated, the initial tension must be added to the load. The result of this calculation is the total load required for the spring.
Force and elasticity also depend on physical size. Follow the exponential formula provided to the compression spring to ensure that your spring is not under too much pressure.
Linear torsion spring
The linear torsion spring is very different from the compression and tension springs because it is not a push/pull action, but a rotation action. But that doesn’t mean they’re not linear. The speed of a linear torsion spring is also constant, and the load applied to the leg of the torsion spring is also proportional to the degree to which it moves under that load.
In rare cases, customers may decide to turn their torsional springs into torsional compression springs by increasing the pitch between the coils. They can also turn the linear torsion spring into a torsion extension spring by simply making a few changes to the torsion spring legs so that they play the hook. These modifications do not make your torsional spring a nonlinear spring, but rather a bilinear spring, depending on whether you choose to use it as a torsional compression or torsional tension spring, since the compression and tension specifications of your spring are also designed to be linear.