Bulk compression springs
As a specialist custom spring manufacturer, we can manufacture bulk compression springs of various types, shapes and materials to your specific specifications.
Bulk compression spring is a kind of mechanical parts that use elasticity to work, will be deformed under the action of external force, when the external force is withdrawn and can be restored to the original state, it is mainly used to withstand axial pressure, the cross section of the material used is mostly circular, but also the use of rectangle and other shapes rolled.
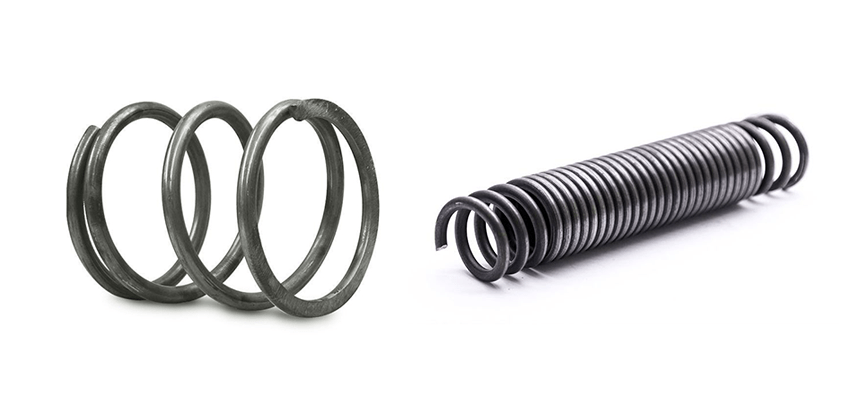
Bulk Compression springs manufacturing steps:
1.Preparation of raw materials
- Selection of materials: According to the use of the Bulk compression springs, working environment and load requirements, choose the appropriate spring steel materials, such as stainless steel, carbon steel or alloy steel, these raw materials have good elasticity, fatigue resistance and corrosion resistance.
- Material inspection: Before processing, the selected material is strictly inspected for quality, including chemical composition, physical properties and dimensional accuracy, so as to ensure that the material meets the design requirements.
2.Processing and forming
- Cutting: According to the required Bulk compression springs length, use cutting equipment to cut the spring steel wire to the corresponding length.
- Cold drawing: Using the plastic deformation of steel wire, cold drawing process, so that the size and strength of steel wire to meet the design requirements. This step can increase the hardness and tensile strength of the steel wire.
- Winding: The automatic spring winding machine is used to wind the cold-drawn steel wire into the required shape, and the winding process needs to control the winding force and speed, so as to ensure the size and shape of the Bulk compression springs.
3.Heat treatment
- Annealing: The annealing treatment is to eliminate the internal profit generated during the winding process and improve the plasticity of the material. Annealing temperature and time are determined according to the type of material and the requirements of the spring.
- Quench and temper: For springs with high hardness and strength requirements, they also need to be quenched and tempered. Quenching is the rapid cooling of the spring after heating to a high temperature, thus obtaining a high hardness characteristic. Tempering is heating at a low temperature after quenching to eliminate quenching stress and stabilize the tissue.
4.Follow-up Procedure
- Section treatment: The section of the Bulk compression springs is polished or cut to ensure its flatness and dimensional accuracy.
- Stress relief annealing: In the subsequent treatment process, it is also necessary to carry out stress relief annealing to further eliminate the residual stress inside the spring.
- Alignment: The spring is straightened or integrated to ensure that its shape and size meet the requirements of the design.
5.Surface treatment
- Anti-corrosion treatment: In order to improve the corrosion resistance and service life of the Bulk compression springs, it is usually necessary to carry out anti-corrosion treatment, such as black oxidation, galvanized, chrome plating or spray anti-corrosion paint;
- Shot blasting: In order to improve the fatigue degree of the spring, shot blasting can also be carried out to deal with surface oxidation and small defects, improve surface roughness and fatigue strength.
6.Quality inspection and packaging
- Quality inspection: Strict quality inspection of the Bulk compression spring, including size, shape, strength, hardness and other aspects of the inspection. At the same time, elastic and fatigue life tests are also required to ensure that it meets the design requirements and use standards.
- Packing: Properly pack qualified Bulk compression springs to prevent damage or contamination during transportation and storage.
The production process of the Bulk compression spring contains the above several steps, each step requires strict control of process parameters and quality requirements to ensure the quality and performance of the final product.