Machined torsion spring
Machined torsion springs are single-piece materials that are precisely designed and processed to have spring characteristics. The design of machined torsion springs provides precise performance, and you can customize the performance characteristics of the machined springs according to the strictest application requirements.
One of the main advantages of using machined torsion springs is the ability to machine connection features into the elastic element and provide solutions that are not easily achievable with wire-wound springs, especially in torsion applications. The design of machined torsion springs can also adopt multiple starting points to solve common problems of traditional springs. For example, squareness and lateral force under load.
Since our springs are processed for specific applications and purposes, they are suitable for high-precision applications and commercial-grade requirements, and can provide excellent elastic performance in various applications. Machined torsion springs benefit the entire system design by enhancing functions, improving accuracy and reducing costs. Time and again, we have used machined spring products to reduce the burden on mechanical systems.
Advantages of Machined Torsion Springs:
- Provide a predictable linear rate to meet the application requirements. 100% repeatable rate.
- Each component provided meets the customer’s precise size and performance requirements.
- The size variation of machined torsion springs is usually much smaller.
- The final component has almost no residual stress, and special or custom end components can be incorporated into an integrated design.
- There are a variety of materials to choose from.
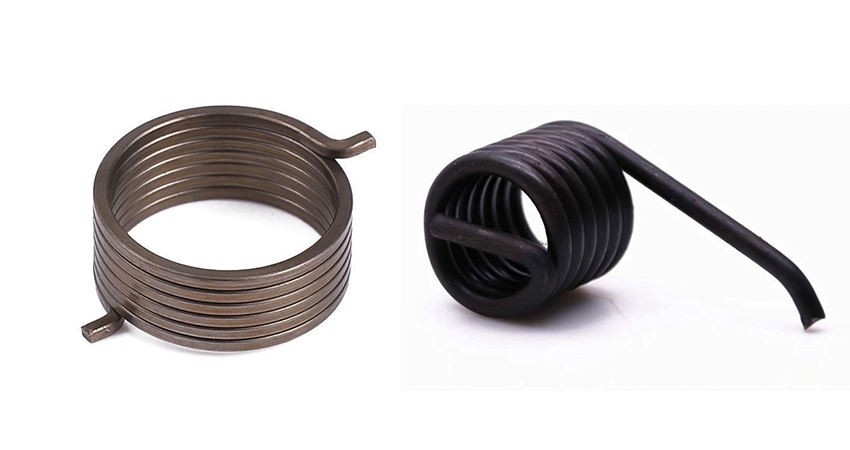
Characteristics of machined torsion spring:
- Machined springs can provide a very precise linear deflection rate because almost all participating stresses are eliminated. The stress in machined torsion springs is mainly pure bending stress, which can provide a more reliable and accurate spring rate.
- Most wound torsion springs can achieve a rate tolerance of about 15%; while machined alternatives can easily achieve a rate tolerance of 10%, and can be adjusted to ±2% for more demanding applications.
- The most common configuration of machined torsion springs is the single-start spring, which consists of multiple continuous coil elements, starting from one end and ending at the other end, very similar to wound springs. We can provide both loosening and winding torsion springs, and in both cases, the spring rate reaches the linearity allowed by the geometry.
- However, the accuracy of the rate is not the only advantage. Since the parts are processed, we can integrate any form of end attachments into the torsion spring. It is important to remember that we can provide attachments integrated with the processed spring in order to solve the pure torque problem.
For machined torsion springs, torque can be applied using pure couples. Some examples of this aspect are double handles (external, internal and longitudinal), slots, splines (internal and external) and bolt circle configurations. Torque can also be addressed by the overall torque constraint on the coil side. How to connect the machined torsion spring usually depends on your imagination. Maybe other components of the system can be incorporated into a single spring system.
However, it is important to remember that the various machining attachments that solve the pure moment are unique.
Machined torsion springs are usually able to replace traditional springs, providing flexibility and mobility, while offering the best support, torsional strength, longer service life and higher flexibility of use through various end rechecking and configuration options. Machined torsion springs are widely used due to their extensive advantages.
Machined torsion springs have high precision and consistency, and can meet the application scenarios with strict requirements for spring performance and size. During the manufacturing process, advanced machine tools and processes are usually used to perform processing operations such as cutting, grinding, and drilling on the raw materials to obtain precise shapes and sizes.