Spiral Stamping Compression Mould Spring
Spiral Stamping Compression Mould Spring is a type of spring widely used in die manufacturing, which combines the energy storage characteristics of spiral spring with the precision requirements of stamping die.
The helical stamping compression die spring is a kind of helical spring that can withstand the desired pressure. Its material cross section is mostly prototype, and it is also made of rectangular and multi-strand steel rayon coil. The spring is generally of equal pitch and has various shapes, including cylindrical, conical, convex and concave shapes. The spring uses a number of open coils to provide resistance to the external load pressure, that is, when the spring is subjected to external force, the spring contracts and deforms, stores the deformation energy, and releases the energy to restore the original state when the external force disappears.
1Pcs Spiral Stamping Compression Mould Die Spring Outer Diameter 20mm Inner Diameter 10mm Length 20-150mm


Function and application:
- The spring of spiral compression die plays a vital role in die manufacturing and is mainly used in the following aspects:
- Buffer and shock absorption: During the die stamping process, the spring can absorb and disperse the impact force, protecting the die and the workpiece from damage.
- Reset and hold: Ensure that the mold can be quickly reset after the stamping is completed, and maintain my preset working state.
- Pressure and support: to provide the necessary support for the mold, to ensure that the mold can still work normally under high pressure environment.
- Spiral Stamping Compression Mould Spring is widely used in automotive, home appliances, instrumentation, building materials, chemical, medical equipment, aerospace and other fields, especially in the automobile shock absorber, engine valve spring, motorcycle shock absorber, clutch and brake components, its importance is self-evident.
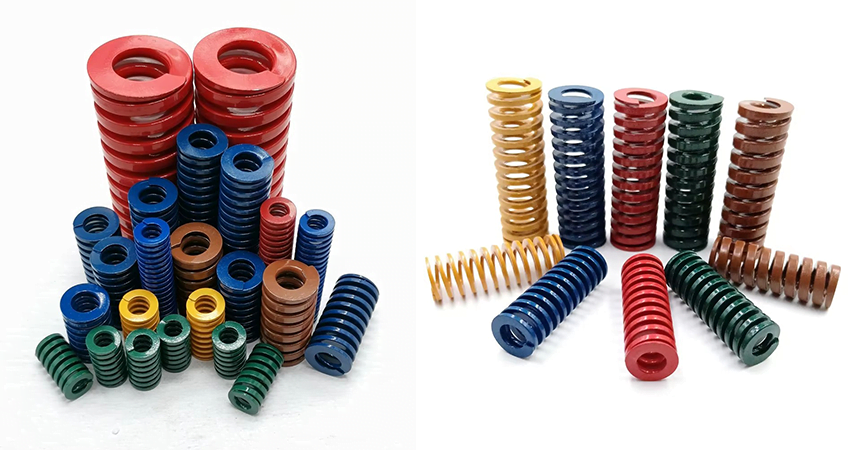
Manufacturing process
- The manufacturing process of Spiral Stamping Compression Mould Spring is relatively complex, mainly including the following steps:
- Coil spring: Winding metal wire into a spiral shape.
- De-stress tempering: eliminate the internal stress generated during the winding process to improve the stability and durability of the spring.
- End grinding: grinding the end face of the spring to ensure dimensional accuracy and surface quality.
- Correction: The shape and size of the spring are corrected to meet the design requirements.
- Surface treatment: anti-rust, anti-corrosion and other treatment to improve the service life of the spring.
Note:
- When choosing a Spiral Stamping Compression Mould Spring, the following factors need to be considered:
- Load requirements: Select the appropriate spring specifications and models according to the impact pressure and working conditions of the die.
- Working environment: Consider the use of the spring environment, such as temperature, humidity, corrosion, etc., select the appropriate material and surface treatment process.
- Life requirements: Select the appropriate spring material and manufacturing process according to the service life and replacement cycle of the mold.
- In addition, when using Spiral Stamping Compression Mould Spring, the following points need to be.
noted:
- Regular inspection: Regularly check the deformation, wear and surface quality of the spring to ensure that the spring is in good working condition.
- Reasonable installation: Install the spring correctly according to the design requirements to avoid failure or damage to the spring due to improper installation.
- Avoid overload: Avoid the spring to bear more than its design load force, so as to avoid plastic deformation or fracture.
The Spiral Stamping Compression Mould Spring is an indispensable component in die manufacturing, and its performance and quality directly affect the service life and work efficiency of the die. Therefore, various factors should be fully considered when selecting and using the Spiral Stamping Compression Mould Spring to ensure that the spring can meet the working requirements of the spring.